“Safety First” is More Than Just a Tag Line
Safety is the first of our six core values and a priority focus on the job sites.
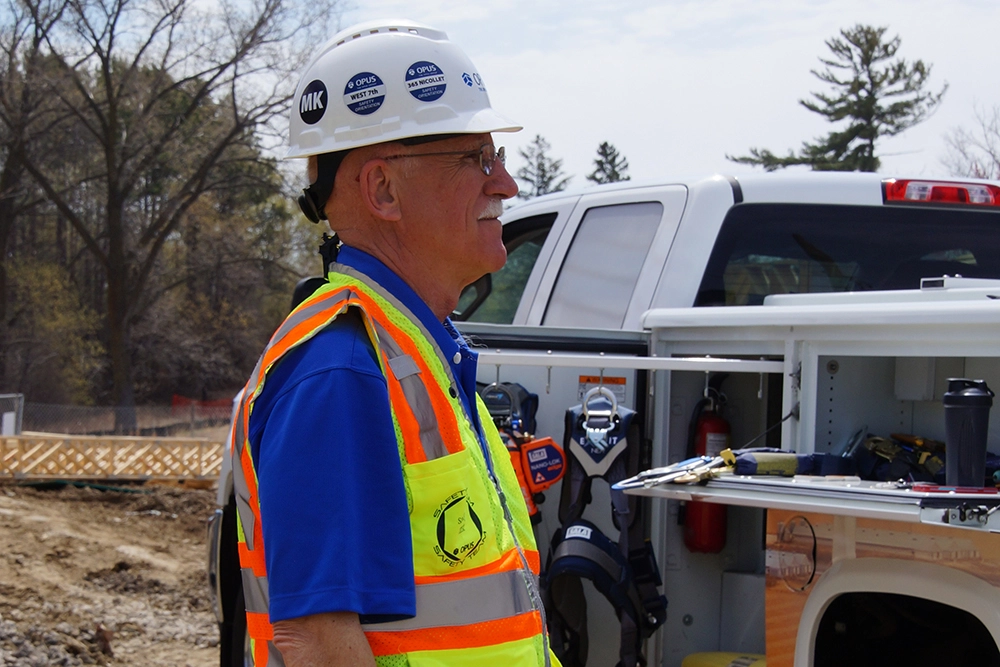
At Opus, we value our skilled field associates who work hard every day at our jobsites across the country. They are essential to delivering quality products to our clients, and we want them to go home safe every day. That's why “safety first" is more than just a tag line for us. Safety is the first of our six core values. It is front and center in our commitment to creating and maintaining an active and effective safety program.
Built into Our Cultural Fabric
“Safety is built into the fabric of our culture and a key component of our everyday operations," said Andy Smoka, director of safety management for Opus Design Build, L.L.C. “We are constantly evaluating the safety of our operations and innovating to find even better ways."
According to Andy, creating a safety culture is the goal; the safety climate is a measurement of progress. “A safety culture is when safety is foremost in everyone's mind 100% of the time, with an ultimate goal of zero safety infractions. Safety climate tells us how we are doing toward that goal, and if our safety culture is improving."
“Safety climate can certainly be measured by OSHA evaluation scores," Andy said. “Opus scores have consistently trended up over the past 10 years, and that's how we know we are hitting the mark and creating a safety culture. We're also often ahead of the curve. For example, OSHA has just begun enforcing its silica standard, but three years ago we started proactively putting new tools and dust management systems in place to mitigate the risk to our associates."
Safety: From the Top Down & Committee Approach
We use a prescriptive approach to encouraging safety in the field, and it starts with senior leadership. “Our leadership team firmly believes creating a safety culture begins at the top. They participate in safety meetings and periodic walk-throughs at our jobsites where they observe and participate in safety-related initiatives happening in the field," Andy said.
Committees also promote and manage safety throughout the organization.
Our safety leadership team and our field leadership team each meet regularly to review and evaluate safety at project sites, working closely with representatives from our project management, legal and risk departments.
A Foreman Safety Committee was also recently formed in Minnesota, where our field foremen from each of our signatory trades meet regularly with a safety associate to discuss safety issues, communication, tools and processes, as well as safety training and policies.
There are also project-specific safety committees, which involve subcontractors. Our associates work with a representative from each subcontractor on the project to do periodic safety checks and walk-throughs. This encourages participation from everyone on the project and strengthens relationships between our subcontractors and our project associates.
“We also do a significant amount of safety training for our associates—both in-house and through third-party providers," Andy said. Associate safety training is important in creating a safety culture. Examples of associate safety training include training to understand OSHA guidelines and the following:
We train associates on OSHA's Construction 30-hour and OSHA's Construction 10-hour classes.
Our associates who operate equipment such as: forklifts, scissor lifts and articulating boom lifts receive certified training in house. In addition, we provide specific third-party certification training for flagging, signaling, rigging and scaffolding.
Foremen and superintendents are certified in first aid and CPR.
“We are continually making improvements to our safety programs and involving more and more people in the process," Andy said. “It's like peeling an onion: we focus on every layer of our operations to ensure they are properly educated about safety and its importance."
Safety Program Recognitions
We are committed to creating a safety culture and our efforts are getting noticed. We have received five Minnesota Safety and Health Achievement Recognition Program (MNSHARP) Construction certifications, which recognize Minnesota companies for outstanding jobsite safety and health practices. We have also received three LECET Safety Driven Awards of Excellence, an award conferred by the Minnesota Laborers-Employers Cooperation and Education Trust recognizing contractors for improving documentation, safety equipment and procedures and hosting dedicated safety meetings or sharing best practices.
Andy Smoka's individual contributions to safety have been noticed as well. “In 2016, I was honored to receive the LECET Safety Spirit Award, which recognizes individuals who have made significant contributions to construction safety in Minnesota." He was just the second person to receive the award in the program's 10-year history.
In addition to directing safety at Opus for two years, Andy has spent countless hours promoting and leading safety and injury prevention programs for the greater construction industry.
Article Type: Blog Post
Topics: Safety