How We Delivered for Hallmark During the Worst Building Material Crisis in Recent History
Despite supply chain and cost escalation issues, we delivered the building on schedule and just in time for Hallmark to take occupancy by their deadline.
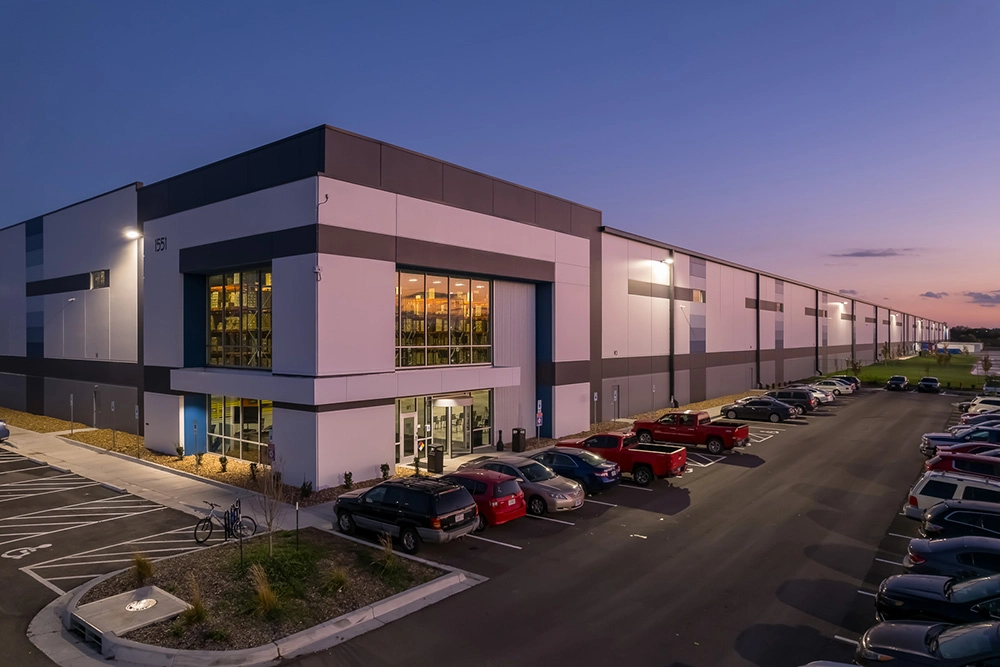
The Project: Hallmark Distribution Center
To boost their logistics capabilities, Hallmark engaged our Kansas City team to develop, design and build an 847,475-square-foot distribution center in Liberty, Missouri, where Hallmark has operated for 50+ years. The expansive distribution center has 40-foot clear height, a 150,852-square-foot structural mezzanine, 47 dock doors, two drive-in doors and a cross-docked warehouse. The main entry features an architectural and glass vestibule and there are office areas, breakrooms, and conference rooms.
Despite a myriad of supply chain and cost escalation issues spurred by the pandemic, we delivered the building on schedule at the end of February 2023 – just in time for Hallmark to take occupancy and receive product by their March 1 deadline.
The Challenge
In October 2021, construction began on the building. Meanwhile, lockdowns and social distancing measures were having a dramatic impact on supply chains, which lasted through 2022 and into 2023.
From day one, we faced an onslaught of challenges procuring vital building materials and services, such as roofing material, structural steel, precast wall panels, concrete service, HVAC equipment and electrical equipment. There were also significant cost escalation issues across the board.
All major roofing manufacturers went to an allocation process, but even then, there were no guarantees they could deliver as promised. Structural steel had lead times of nine months and costs were increasing weekly. The same was true for precast wall panels. Meanwhile a shortage of concrete truck drivers was putting production of the slab on grade at risk. And suppliers for HVAC equipment and electrical switchgear equipment were unable to fulfill orders until well after the scheduled project completion date.
The Solution
“Procurement of roofing material was undoubtedly one of the biggest obstacles we had to overcome," said Megan Garner, Project Executive.
It started with roofing insulation (polyisocyanurate). In late spring 2022, we were informed that only a limited number of truckloads would be available each month. For a building this size, 1.7 million square feet of insulation was needed.
“It became clear we wouldn't receive all the required insulation until after the scheduled project completion date," said Megan.
Issues with the thermoplastic polyolefin (TPO) membrane and fasteners quickly followed. Hundreds of thousands of fasteners were required for this project. All of this put the project's schedule in jeopardy, as many critical path activities follow the roof installation.
“We tackled the roofing problems on all fronts," said Megan. “Our design-build and development team members networked with business connections and Opus colleagues in other areas of the country. A strong lead out of Arizona was able to provide us with two-thirds of the roofing insulation required within just a few weeks. Later, we sourced 73,000 square feet of roof membrane from them."
Due to the short supply of roofing materials from the original manufacturers identified, other manufacturers' products had to be considered to keep the project on schedule. The project team established good lines of communication and evaluated alternatives. That included installing polyvinyl chloride (PVC) roofing membrane on a portion of the roof in lieu of the typical TPO roofing membrane.
“We got quick feedback from the manufacturer, our development team, Hallmark and the building insurer in a matter of a few emails," said Megan. “We were able to maintain the original manufacturer's warranty for the roof system, which was a critical component for all parties involved."
“To watch how the Opus and Hallmark teams worked together dealing with the challenges head on was incredible – it was a really close collaboration," said Michael VanBuskirk, Vice Chairman & Principal, Newmark Zimmer, who represented Hallmark on the project.
The roof was completed in August, allowing slab-on-grade work to commence, keeping the project on schedule.
“As soon as the roof was on, we were off to the races pouring the slab-on-grade," said Megan. “We were able to get 850,000 square feet poured in a matter of a few weeks, despite the shortage of concrete truck drivers. Our site superintendent, Brian Eckart, did a masterful job of strategizing with the concrete subcontractor well before the roof was completed."
Given the shortage of structural steel and precast, we mitigated risk by committing to the scope early with fabricators. Joist girders were also in short supply since there are very few suppliers. Lead times were much shorter for wide flange beams. So, our in-house engineering team quickly prepared an alternate design using the beams. At the time, the beams were also less expensive than joist girders, which provided a cost savings.
We worked with our HVAC subcontractor to identify and engage an alternate manufacturer for the rooftop HVAC equipment. Procuring electrical switchgear equipment was also a problem. By working closely with the local electric utility company, we devised a temporary, overhead option for providing power to the building that required minimal switchover time once the utility company's switchgear equipment became available.
Throughout the project, persistent cost escalation threatened the budget and timelines.
“There were many instances when we hadn't yet released a scope of work and were suddenly faced with impending cost increases," said Megan. “Our teams had to act quickly to gather the required approvals and release the scopes ahead of the price hikes. That required a total team effort from our construction team, our development team, our design team and Hallmark. It's a great example of the value our vertically integrated, one-team model brings to projects."
“The true value that Opus brings to the equation is having all seats at the table," said Oscar Healy, Regional Vice President of Construction. “We've got the developers, project managers, architects, engineers and field supervisory folks. That makes us nimble. We can analyze, plan and make recommendations early to ensure the needs of our clients are met."
There were much longer than normal lead times for many building materials not mentioned above, such as dock equipment, overhead doors and interior switchgear equipment. We started the clock early and had the equipment under contract as soon as possible.
“It was a perfect storm of the pandemic and the most significant material crisis any of us have experienced," Brian said. “We had to get creative to weather it, knowing that Hallmark was on a very tight time crunch in terms of delivery date, getting moved in, and being fully functional in the building."
The Result
Despite relentless supply-chain disruptions and unexpected curveballs, our team delivered the Hallmark building on time.
“It was a tough climate in which to deliver such a large project," said Megan. “We had great working relationships with Newark Zimmer, the City of Liberty, Hallmark, and our various subcontractors and partners. Those relationships made all the difference when navigating the influx of obstacles along the way."
The custom-designed building represents a significant milestone for Hallmark. It increased the company's logistics footprint by 50%, enabling new capabilities and efficiencies as Hallmark continues to meet the changing needs of its customers.
“The fact the project was delivered within days of what our anticipated delivery day was when we signed the lease is amazing to me," said Brian. “That just goes back to the advantages of Opus' design-build model. I'm very satisfied with this project how it turned out. I smile every time I drive up to it."
Article Type: Case Study
Topics: Industrial Development & Construction | Kansas City | Projects