Opus Delivers for Renewal by Andersen Despite Complexities
Our team addressed multiple challenges to deliver an expansion for Renewal in Cottage Grove, Minnesota.
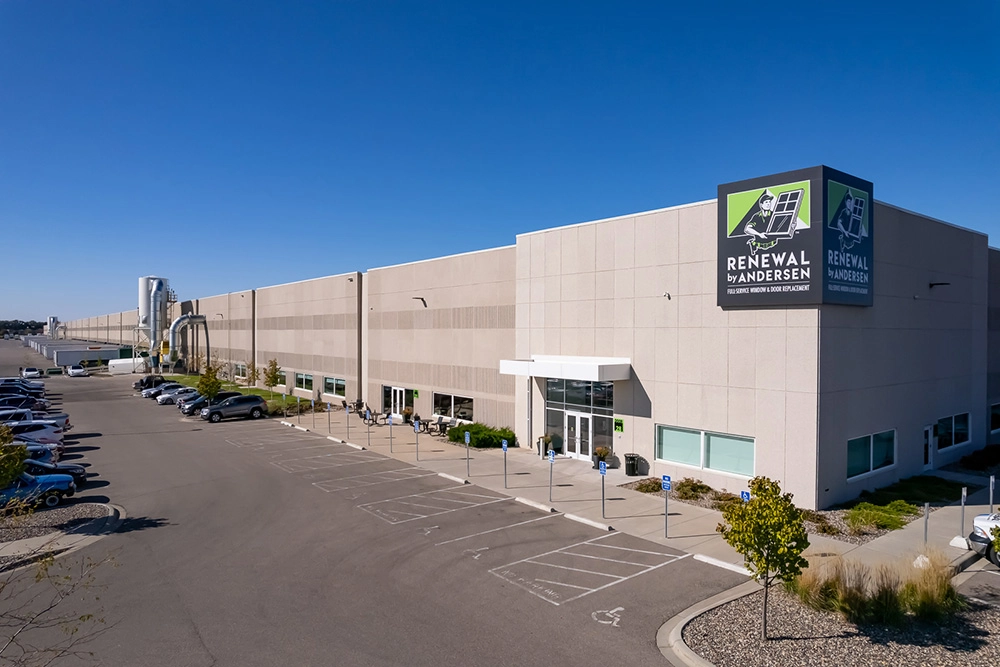
The Project: Renewal by Andersen Value Add Center
Due to steady growth, Renewal by Andersen was outgrowing its assembly plant in Cottage Grove, Minn. They needed more warehouse, office and training space, as well as room for better sequencing of manufacturing processes and future line expansions. The window replacement subsidiary of Andersen Corporation chose Opus to develop, design and construct a new 350,000-square-foot facility adjacent to the existing assembly plant. Opus delivered the building in June 2020.
The Challenge
Renewal by Andersen chose Opus due to their track record of delivering state-of-the-art buildings custom designed for specific manufacturing operations, as well as their ability to execute expeditiously with the City of Cottage Grove. The new building was in very close proximity to their existing, extremely busy manufacturing plant, so it was imperative that construction activities and related sequencing of operations did not disrupt any operations for Renewal by Andersen.
Therein lied the challenge.
“The unique needs that came with this project we trying to develop a new building, right adjacent to an existing operational facility and not impact their day-to-day operations," said Jay Fourniea, Director of Architecture.
Renewal would need to continue their operations throughout construction.
The Solution
To ensure minimal disruption, Opus prepared and executed a project work plan and coordinated all construction activities that would or could potentially affect Renewal by Andersen's operations. Opus also constructed a link structure that tied the two buildings together, providing convenient transfer for employees, equipment and materials. Much-needed access to parking for Renewal by Andersen trucks and trailers was arranged in the newly constructed parking lot, even during grading and paving operations.
When the pandemic hit in Minnesota, nearly three months of construction remained. Disruption management planning became an even bigger challenge and more important. Opus collaborated closely with Renewal by Andersen teams, working together to balance new safety protocols, conduct contact tracing and coordinate access between the existing facility and the construction site. The environment was changing quickly due to the pandemic, and Renewal by Andersen recognized Opus' ability to adapt quickly and make necessary scope modifications mid-construction.
“With their building experience, they were very good at telling us what could work and what we should steer away from," said Mike Steen, Andersen's Maintenance Manager. “They had our best interests in mind always. From the leaders on down to site superintendents and foreman, they are all very respectable, intelligent and very personable."
The Result
From the time the project broke ground to when Renewal by Andersen cut the ribbon was less than a year. According to Paul Delahunt, President of Renewal by Andersen, who is now retired, it took only a few months to start seeing the benefits of increased efficiencies, reduced inventory and handling and more flexibility in manufacturing.
“A new manufacturing campus is a significant investment," said Linda Larson, Director, Real Estate Services for Andersen Corp. “Opus proved themselves reliable and able to pivot when we needed to pivot. Every curveball that we threw them, they just hit it out of the park."
Andersen's Chairman and CEO Jay Lund added, “We couldn't be more pleased with the outcome of this project. Opus completed everything on time and on budget. Plus, they have just been easy and a great partner to work with at every stage of the process."
Article Type: Case Study
Topics: Projects