Opus’ Integrated Approach Delivers Speed & Technical Expertise
When North Star Sheets needed an aggressive schedule for delivery of an industrial building designed specifically for their unique business needs, they enlisted our team.
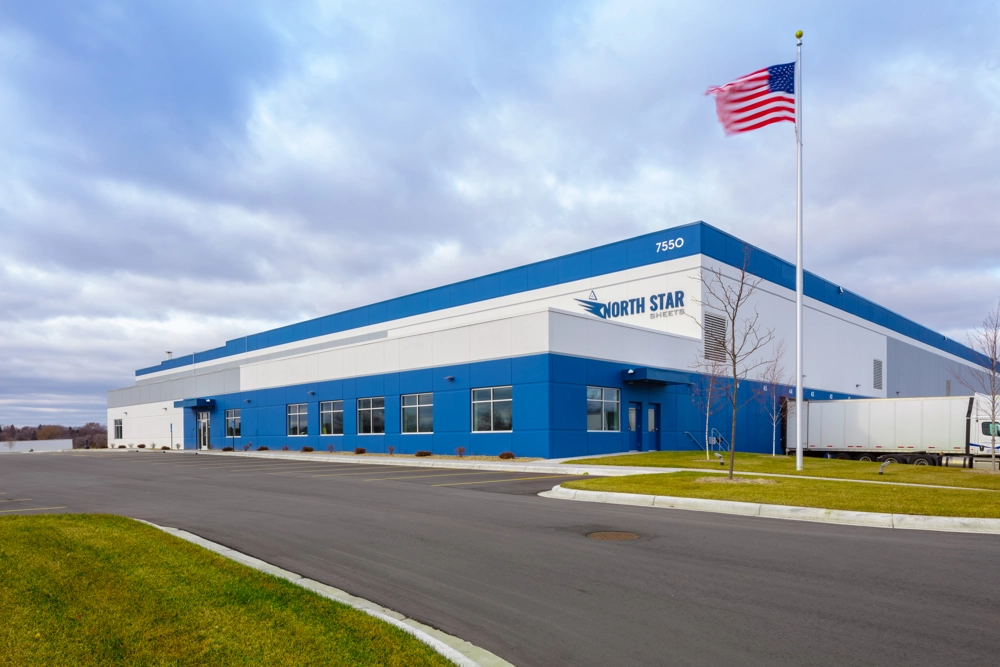
When North Star Sheets needed an aggressive schedule for delivery of an industrial building designed specifically for their unique business needs, they enlisted Opus.
A Schwarz Partners company that manufactures corrugated cardboard sheets, North Star Sheets expanded their operations into Minnesota. To support their growth plans, Opus developed, designed and constructed a 161,000-square-foot manufacturing facility on a rail-served, 16-acre property in Cottage Grove, Minnesota.
Speed of Delivery
Opus delivered the build-to-suit project on a condensed construction timeline. North Star Sheets initially contacted Opus about the property and project in late December 2017, and moved their equipment in early August 2018 – just over seven months from project conception to start of equipment installation.
The North Star Sheets project exemplifies how Opus' design-build approach to project delivery makes it possible to fast-track projects without sacrificing quality. It's different from a traditional design-bid-build process managed by a general contractor because Opus brings a full staff of development, architecture and construction experts to the table. All stakeholders are integrated from day one, until the last building detail is finished. It's a holistic, client-centered approach to project delivery that brings greater value to clients by maximizing efficiencies, quality and budget.
In January 2018, Opus started the North Star Sheets project like it does all projects – by listening to the client and fully understanding their goals and vision for the future. In addition to conducting multiple listening meetings, Opus sent a team to a comparable Schwarz Partners facility in Indiana to study how a similar corrugated sheets production facility operates and is used. By the third week in February, the preliminary design for the Minnesota building was finalized, a guaranteed maximum price was established and a contract was executed.
Expediting government approvals and gaining community support for projects is a key area of expertise at Opus. Approval for the North Star Sheets project was gained just eight weeks after the initial meeting with the city, and the building permit was issued shortly thereafter on March 22. Opus organized all resources and worked judiciously with the planning department, planning commission and city council to accelerate the process for approval of site plan and zoning variances.
Wasting no time, Opus crews started earthwork and foundations the first week in April. Despite several significant late spring snowstorms and the snowiest April on record in Minnesota, the project remained on track for an early August equipment installation and became fully production operational the first of September.
Much of the project's construction speed of delivery can be attributed to using the Last Planner System™ on industrial facilities. The team was able to gain weeks of time efficiencies through collaborating during pull planning sessions with all contractors on the construction site to determine the quickest and safest way to build the project.
Technical Expertise for Specific Requirements
By listening carefully to North Star Sheets' requirements for the building, Opus identified the best combination of bay sizes, column spacing and clear height to meet operational needs, while keeping the building design cost efficient. In addition, Opus mitigated several potential issues related to technical complexities that are unique to the client's operations.
Due to North Star Sheet's past negative experiences in non-Opus constructed facilities, the company had concerns about floor slab performance. The Opus team analyzed the issues and presented technologies that would better handle the loads and work conditions, such as maximum control joint spacing of up to 100' on-center, a concrete mix design with crack reducing additives and integration of steel reinforcing fibers.
By understanding the specifics of North Star Sheets' operations, Opus also presented an approach for performing specialty concrete work to accommodate production equipment, like a variety of foundation pads, recessed slabs, trench drains and utility pathways. Opus also engaged electrical and mechanical experts to design a more efficient means of feeding power to various equipment systems and a more cost efficient and simpler operating power control system for HVAC equipment.
***
The integrated team of professionals at Opus employs a unique approach to design-build that focuses intently on client-centered collaboration. The result is customized project solutions and faster schedules, which ultimately enables the client to accelerate achievement of their business goals.
Article Type: Case Study