Rapid Delivery, a High-Quality Building: Delivering for Renewal by Andersen
Tight timeline? No problem. Our multidisciplinary team is experienced at rapid deliveries, including on an industrial expansion in Cottage Grove, Minnesota.
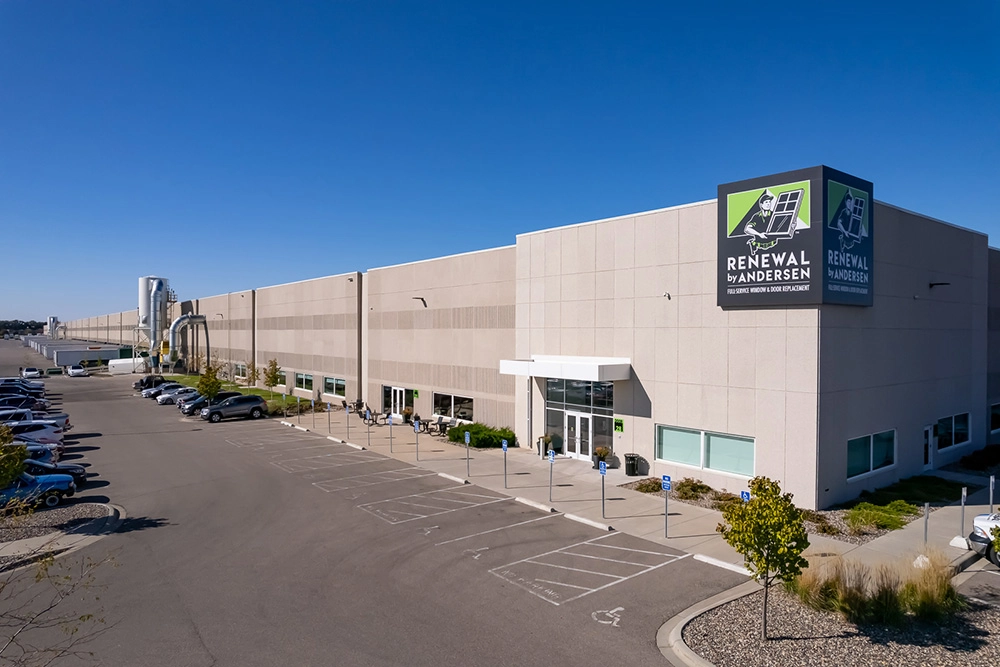
When companies decide to expand their manufacturing operations, they are often already at, or approaching, maximum capacity within their existing facilities. They recognize that production constraints have the potential to impact customer satisfaction, revenues and the company's reputation, and they need to act fast.
Such was the case for Andersen Corporation's Renewal by Andersen replacement window and door division. Its Cottage Grove, Minn., manufacturing facility was maxed out. The company needed to expand its manufacturing, warehouse and office space – quickly – to keep pace with increased demand for its product lines.
Andersen chose us to expedite the design and construction of its new Value Add Center, adjacent to its existing facility.
Expedited Delivery
The project timeline was aggressive – 11 months from start to finish. To deliver a project of this scope in that timeline, it was essential to have the main team – construction, design and development – under one roof.
“The design-build model is really built for delivering at a pace that meets the client's needs," said Jay Fourniea, Director of Architecture. “Ultimately, it delivers the value that they need to continue their mission."
Clients really benefit from a single source of responsibility for all aspects of the project.
“One of the biggest priorities for us was speed," said Paul Delahunt, retired President of Renewal by Andersen. “From the time we broke ground to the time we were cutting the ribbon was less than a year. Our project was actually delivered a little early and a little under budget, which is always a welcomed thing."
Andersen had a single partner from start to finish for the project.
“When we needed to pivot quickly, we only had one partner to go to," said Linda Larson, Director of Real Estate and Administrative Facilities for Andersen Corporation. “We were able to literally shave weeks and weeks off our schedule by having the design continue while we were doing the site work, while we were getting the footings and foundations in place. We were designing as we were constructing."
Supporting Andersen's Mission
Since completing the project, Renewal by Andersen has gained more control of its supply chain by bringing more component production in-house, cutting and storing lineal parts, and reducing the handling of parts and inventory.
In addition to speed, Andersen needed a quality facility that delivered value by supporting their mission. Again, our integrated design-build approach was key. Deep shared expertise between the development, design and construction teams enhanced the process and the final product. This highly collaborative approach helped minimize problems and quickly resolve any problems that arose.
Linda said, “Opus' integrated approach of develop-design-build was exactly what we needed to bring the project to fruition. Their expertise, knowledge and relationships already in place in Cottage Grove really helped facilitate our project and get it over the goal line as quickly as possible."
Watch a video to see how we delivered for Renewal by Andersen!
Article Type: Video
Topics: Industrial Development & Construction | Minneapolis | Design-Build Process | Projects | Expertise