Design-Build: Formidable Site Work Couldn’t Prevent Alsip Park 294 Development
An infill site in suburban Chicago proved to be one of the most challenging development projects our team has undertaken, and its successful completion is credited to our integrated design-build approach.
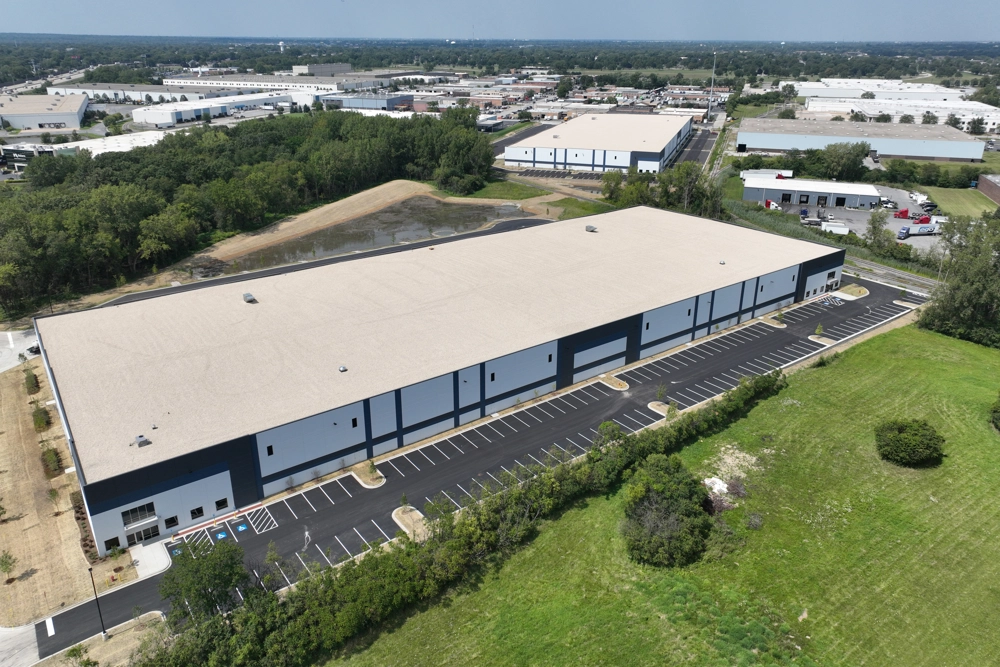
To prevent sprawl, leverage access to existing infrastructure, support revitalization and boost property tax revenue, more and more cities are open to urban infill developments to bring new, modern buildings to vacant or underutilized property within their city limits. Given the general scarcity of smaller urban modern industrial space as well as growing buyer and tenant demand to reduce transportation costs, build-to-suit and speculative industrial projects, in particular, are well poised for infill success.
But this work is not without its challenges as infill sites often include environmental challenges, aging or undersized infrastructure, existing traffic issues or existing building structures that developers must contend with. Nearly all of these challenges were in play with Alsip Park 294, a two-building speculative industrial project we developed on a 22-acre suburban Chicago infill site. In addition, the seller needed to maintain control of the property and could only provide very limited access during the due diligence period.
According to our team, without the flexibility and built-in collaboration of our design-build approach, this project couldn’t have successfully advanced.
The seller, a local radio broadcasting company that had six radio towers and a support building on the site, remained operational for more than 10 months after the purchase agreement was signed, which limited our ability to perform a thorough physical due diligence on the property. While not ideal, the bigger issue was that under each radio tower was an extensive underground grounding system made up of hundreds of heavy-gauge copper wires – wires that couldn’t be disturbed while the radio station was operational. This meant we could either develop our site plans and pursue the necessary permits with very limited subsurface information or we could hold on the design and permitting process until after the radio towers were removed in order to perform the traditional subsurface due diligence before pushing the project forward, causing a 10 month project delay. Our design-build process and transparent contract structure enabled us to take the former approach.
As a vertically integrated team with the ability to share the risks of uncertainty, we identified every potential variable and risk of these unknowns, and then game-planned all the potential outcomes to provide confidence to the ownership team to move forward in this unique way, cutting many days and months out of the overall schedule without negatively impacting the project’s quality or cost.
After construction started, we quickly determined groundwater levels, clay and topsoil quantities and soil bearing capacities; located areas of minor environmental concern; and put several preplanned strategies in action to stay on schedule and budget. We over-dug stormwater detention ponds and added berms to loose excess topsoil, adjusted the building pad and dock elevations to handle clay shortages and bearing capacity surprises, and re-engineered the stormwater drainage systems on the site to make all the new building pad and dock elevations work, all while avoiding additional costs associated with these changes.
Our site earthwork took place in the early winter, when the wet and cold weather make certain types of clay soil impossible to compact for use under building pads and pavements. To avoid the costs and construction downtime associated with shutting down our cut / fill earthwork operations, we used a lime stabilization method to dry and strengthen the clay so that we could complete our earthwork by early winter and not shut it all down until the spring.
Our environmental assessment identified more wetlands on the site than we originally estimated, which required us to relocate the two future buildings to avoid impacting these newly identified wetlands (avoiding major costs and project delays). The optimal new location required moving both buildings closer to an active rail spur, which further dictated the need for building grade changes. We succeeded not only in accommodating those grades to work with these new constraints, but, in the process, created a detention pond between both buildings – all without losing any leasable square footage.
Ultimately, we succeeded in turning an underutilized and challenged brownfield property near downtown Chicago into a modern 360,026-square-foot two building speculative industrial development that we completed in just 10 months, and we delivered $550,000 of savings to the owner at project completion.
Article Type: Blog Post
Topics: Development | Construction | Chicago